Manufacturing technologies
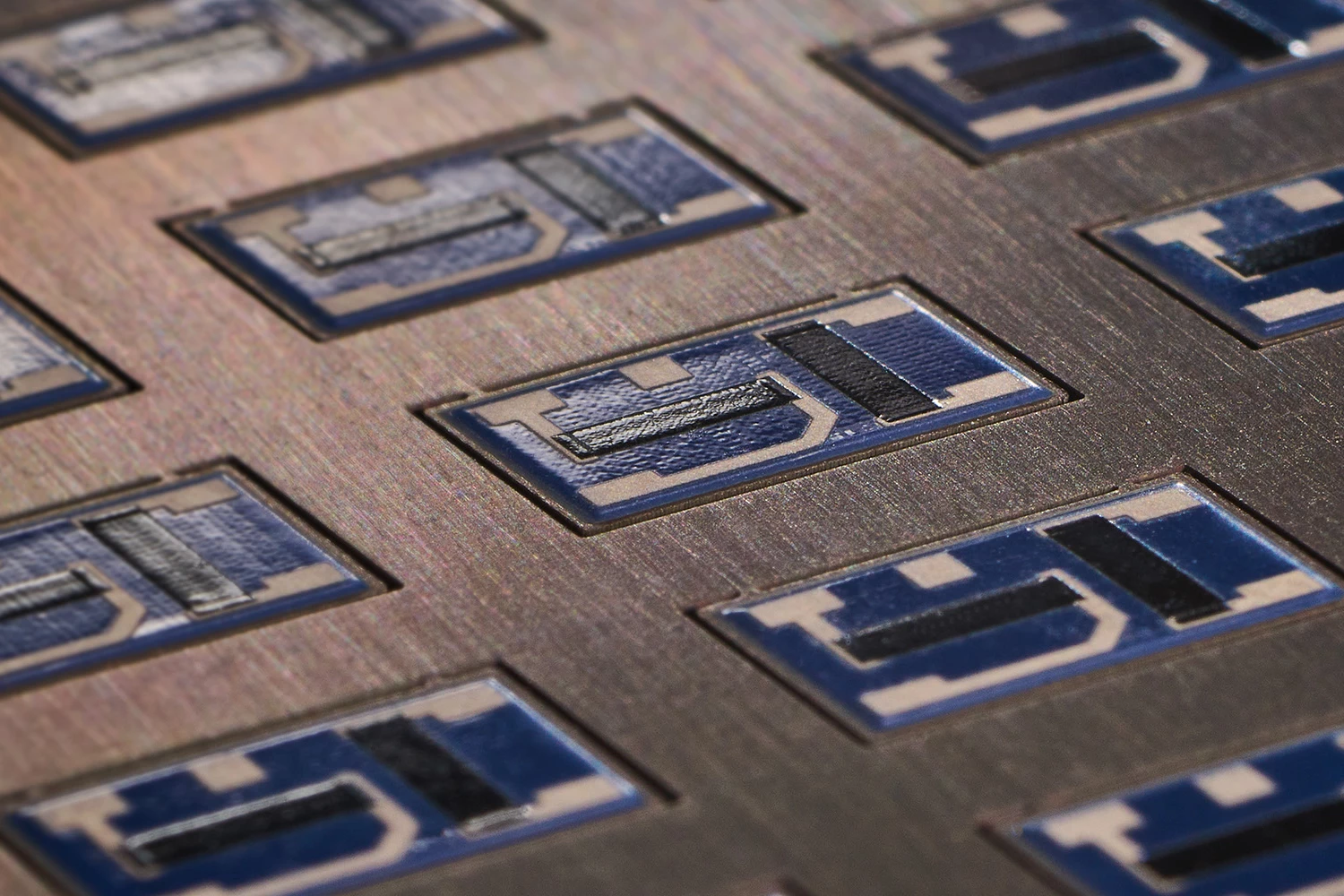
Thick Film Hybrid technology
Thick film technology is a additive mounting and joining technology that allows production of electronic circuits on a variety of base materials (substrates) such as aluminum, steel, ceramic materials (AlN as well as our standard Al203) and glasses.
In a screen printing process, paste-like inks containing metallic, metal-oxide and/or glass frit particles are applied to the substrate and fired to deposit conductive traces, insulating and passivating layers, resistors, capacitors and spiral-shaped inductive features in varying thickness.
This technology for the production of customer specific thick film circuits is implemented as a clean-room process on very modern machinery.
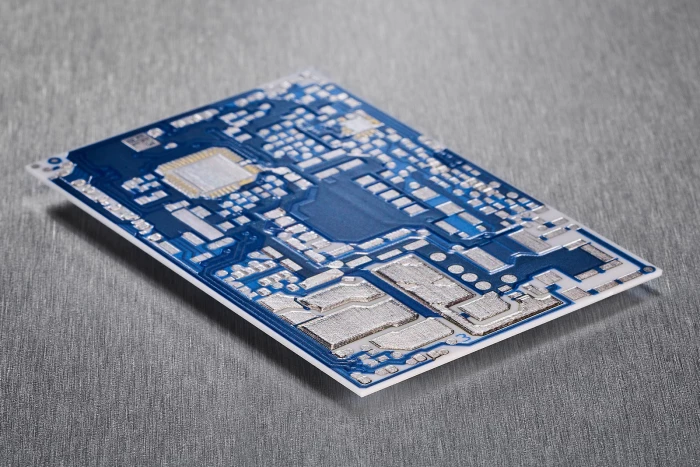
SMD placement
In SMD placement, electronic components are placed on the surface of PCBs (rigid, flexible, combined, metal-core…) or thick film circuits by automatic pick-and-place machines, and reflow soldered. In contrast to conventional mounting of wired components (“through-hole technology” THT), parts are directly soldered to contact pads on the substrate surface instead of using wire pins inserted in circuit board holes.
After solder paste deposition by stencil printing and component placement, boards are soldered in a reflow process with nitrogen inertisation and, if necessary, vacuum treatment for minimization of voiding. Depending on application, components can also be mounted by means of conductive adhesives.
SMD placement currently is the most important technology in populating electronic circuit boards.
Three fully automatic processing lines allow us to place components, some of which are barely visible to the unarmed eye, with maximum precision and speed.
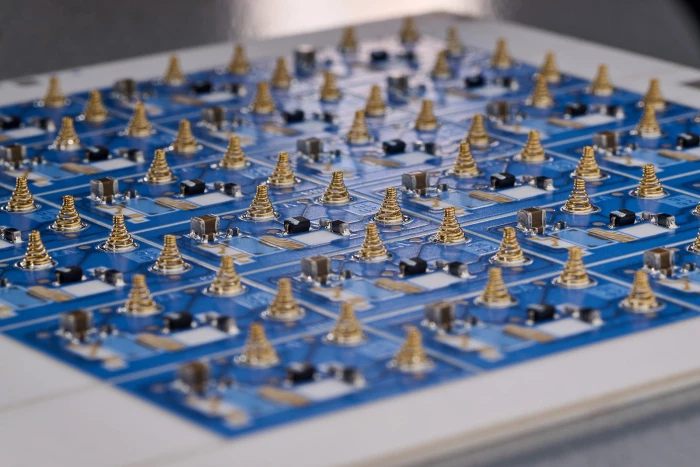
Selective soldering
Selective soldering is an automated 3-D soldering process that is defined by localized soldering of connections in a circuit board.
It is employed when THT components are to be mounted on boards which cannot be manufactured by regular soldering processes due to complex mechanical shapes or additional SMD population on the THT solder side.
Three modern selective soldering machines allow for clean and uniform soldering and assure quality in an optimized series production.
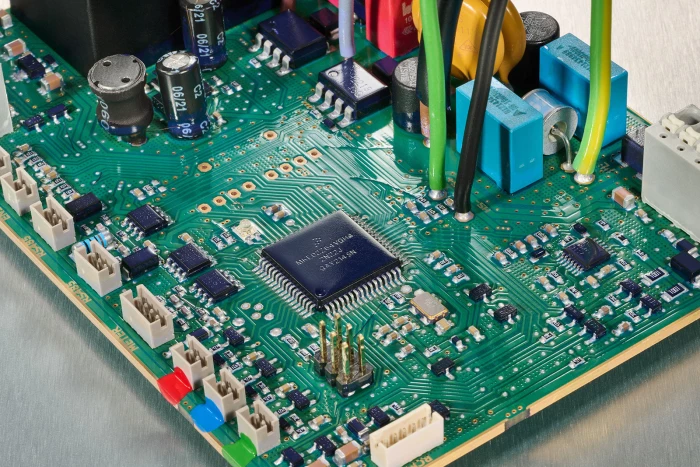
Die and wire bonding
Die bonding is the automated mounting of sensor chips or other unencased semiconductor components on circuit boards. Dice are picked from waffle packs or directly from wafers and mounted on the respective substrate by means of solder or (often electrically or thermally conductive) adhesives.
Wire bonding is a process step that establishes connections between integrated circuits / semiconductor dice and the substrate, neighboring dice, or conductive elements incorporated in the housing they are monted on or in, by means of exceedingly fine gold or aluminum wires. It is a crucial method for miniaturization, power electronics applications, and micro-system assembly. It is a highly reliable and space-saving alternative to soldered connections.
Modern machinery, adherence to IPC framework and clean-room conditions allow us to produce highly reliable components and modules.
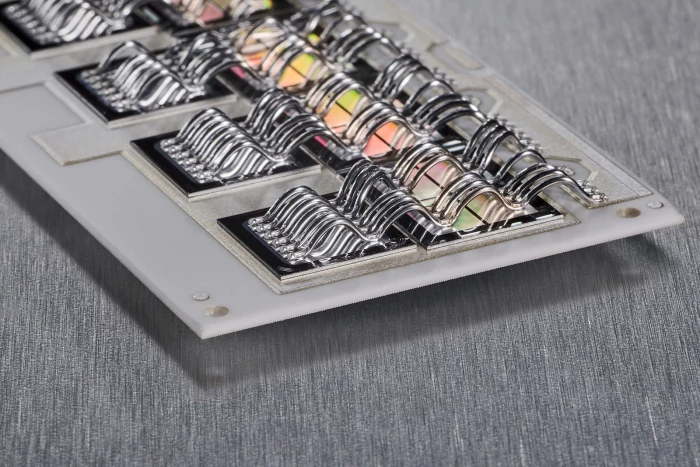
Potting and varnish coating
Populated boards (PCB or hybrid circuits) can be coated with a protective lacquer to improve vibration, condensation, humidity and contamination resistance. Complex customer-specific modules can be potted with a wide range of e.g. silicone or epoxy materials.
Dispensing systems in specially designated areas allow for processing according to automotive-industry standards under perfectly adjusted environmental conditions.
Customer-specific module assembly solutions
Combining an electronic circuit, its housing, and additional materials into a functional module can be accomplished in-house due to a variety of machines and processes together with the necessary technological know-how. Often all of the processes named above, complemented with product-specific machinery, are employed.
For several high-runner products, automated production lines have been realized to guarantee quality and required throughput through the use of modern production equipment combined with high performance robotic handling systems.
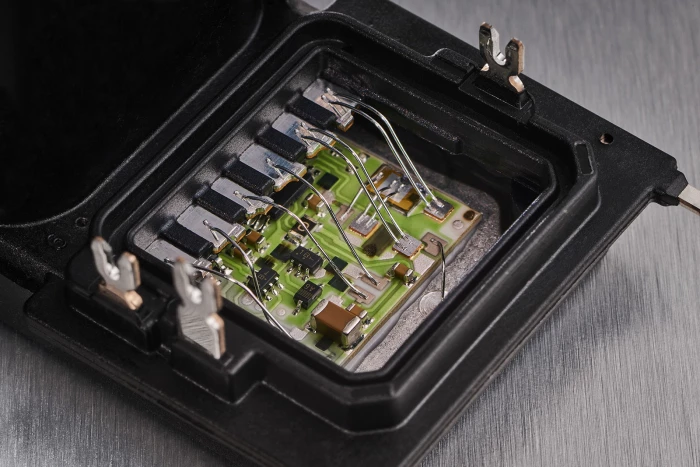